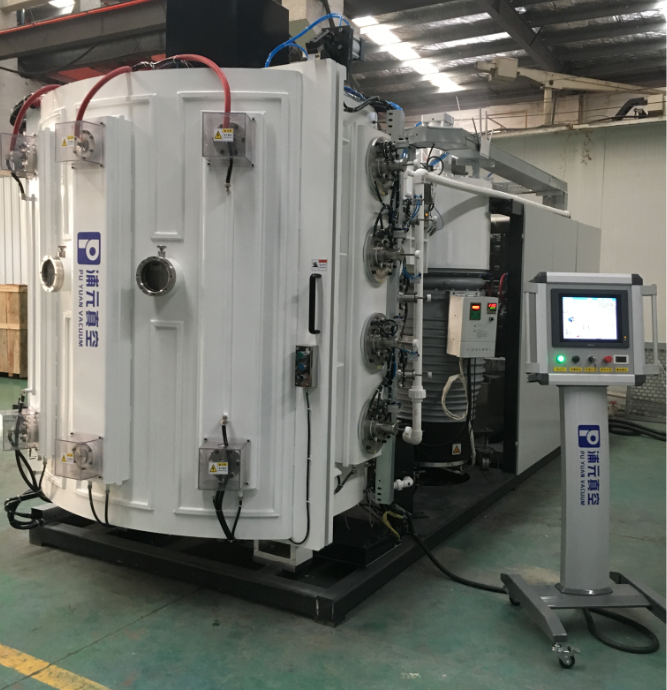
一. 多弧离子镀膜的特点1. 高离化率与高结合力
电弧放电产生的等离子体离化率可达60%~90%,离子能量高(10~100 eV),使膜层与基体形成冶金结合,附着力远超传统电镀或化学镀。
典型应用:刀具镀TiN(氮化钛)时,结合力可达70 N以上,避免膜层剥落。
2. 高沉积速率与均匀性
沉积速率可达1~10 μm/min,是溅射镀膜的5~10倍,适合工业化批量生产。
通过多靶布局和工件旋转技术,可实现复杂形状(如螺纹、凹槽)的均匀镀膜。
3. 低温工艺适应性
基体温度通常控制在200~500℃,避免材料退火变形,适用于塑料、铝合金等低熔点基材。
案例:塑料眼镜框镀仿金属膜时,基体温度低于300℃,保持塑料结构稳定性。
4. 材料多样性
可镀金属(Ti、Cr、Zr)、合金(TiAl、CrAl)、陶瓷(TiN、Al₂O₃)、多层复合膜等。
创新应用:DLC(类金刚石)膜用于发动机活塞环,降低摩擦系数。
5. 环保与高利用率
无化学废液排放,靶材利用率达60%~80%(磁控溅射仅30%),符合绿色制造趋势。
二、行业场景应用及典型案例1. 切削工具与模具行业
需求:提升硬度(HV 2000~3500)、耐磨性、抗高温氧化性。
涂层方案:硬质合金刀具镀TiAlN(耐温800℃),寿命提升3~5倍。注塑模具镀CrN,降低塑料粘附,脱模效率提高30%。
2. 装饰镀膜领域
需求:色彩多样化(金色、黑色、枪色)、耐腐蚀、抗指纹。
应用案例:智能手表表壳镀ZrN(仿金色),通过100小时盐雾测试。汽车门把手镀TiCN(枪灰色),结合PVD与UV底漆技术,实现渐变色彩。
3. 航空航天与能源
挑战:极端环境下的抗高温(>1000℃)、抗冲蚀。
解决方案:涡轮叶片镀MCrAlY(金属-陶瓷复合膜),耐温提升至1100℃。燃料电池双极板镀Cr/CrN多层膜,导电性>80 S/cm,耐腐蚀电流<1 μA/cm²。
4. 电子与半导体
需求:导电、电磁屏蔽、耐电弧侵蚀。
案例:手机中框镀AlTi(导电膜),表面电阻<0.1 Ω/sq。继电器触点镀AgCu合金,电寿命从10万次提升至50万次。
5. 医疗器械
需求:生物相容性(ISO 10993认证)、抗菌性。
应用:骨科手术器械镀TiN-Ag复合膜,抗菌率>99.9%。人工关节镀DLC膜,摩擦系数<0.1,延长使用寿命至20年。
三、技术局限性及应对表面粗糙度问题:电弧镀膜易产生微米级液滴,导致Ra 0.1~0.5 μm。
改进方案:磁过滤电弧技术(如FCVA)可将液滴减少90%,Ra降至0.05 μm,满足光学元件需求。
复杂结构镀膜死角:通过脉冲偏压(10~50 kHz)增强等离子体绕镀性,实现深孔(孔径比>5:1)均匀镀膜。
四、未来趋势复合工艺:多弧镀+HiPIMS(高功率脉冲磁控溅射)制备纳米多层膜,硬度突破40 GPa。
智能化控制:引入AI实时监控电弧稳定性,沉积速率波动从±15%降至±5%。
新兴领域:氢燃料电池质子交换膜镀Pt催化剂层,降低贵金属用量50%。