PVD process
Coating technology and process coating technology and process coating technology and process coating technology and process 1. vacuum coating technology development Vacuum coating technology is not a long time to start, the international community in the sixties of last century before CVD (Chemical Vapor Deposition) technology has been applied to carbide tools. As the technology needs to be carried out at high temperatures (process temperature higher than 1000 º C), coating a single species, the limitations of large, therefore, its initial development is far from satisfactory. By the late 1970s, PVD (physical vapor deposition) technology began to appear, creating a bright future for the vacuum coating a new world, after a short period of two to three decades PVD coating technology has been rapid development, The reason is because of its vacuum-sealed cavity in the film, almost no environmental pollution problems, is conducive to environmental protection; because it can get bright, luxurious surface, in color, the mature color, silver, transparent color , Golden yellow, black, and from golden to black between any color, can be described as colorful, to meet the various needs of the decorative; and because PVD technology, you can easily get other methods difficult to obtain high hardness, high resistance Wear-resistant ceramic coating, composite coating, used in the tooling, mold above, you can make life doubled, better to achieve a low-cost, high-yield effect; In addition, PVD coating technology with low temperature, Features, can be formed on almost any substrate, therefore, the scope of application is very broad, its rapid development is not surprising. Vacuum coating technology has developed to today also appeared PCVD (physical chemical vapor deposition), MT-CVD (medium temperature chemical vapor deposition) and other new technologies, a variety of coating equipment, a variety of coating process after another, now in this field , Has shown a hundred flowers blossom, a hundred contend for the gratifying scene. At the same time, we should also clearly see that the vacuum coating technology development is a serious imbalance. As the tool, mold working environment is extremely bad, the film adhesion requirements, much higher than the decorative coating. Thus, although the decorative coating manufacturers have been all over the place, but can produce mold coating manufacturers are not many. Coupled with the lack of tooling, mold coating service, so far, the majority of domestic coating equipment manufacturers can not provide a complete tool coating technology (including pre-treatment process, coating process, coating process, testing Technology, coating tools and mold application technology, etc.), but it also requires the technical staff, in addition to proficient in coating expertise, it should have a solid knowledge of metal materials and heat treatment, mold coating before the surface pretreatment Knowledge, tool, mold coating and the reasonable choice of the technical requirements on the machine, if any part of the problem, will give users the results are not ideal to use such a conclusion. All of these have seriously restricted the technology in the tool, mold application. On the other hand, because the technology is a new material science, physics, electronics, chemistry and other disciplines of the emerging edge of the discipline, and its domestic application of cutting tools, mold production in the field of a few key manufacturers, Most of them take a road from abroad to introduce advanced equipment and technology, still need a digestion and absorption process, therefore, the current domestic technology in the field and its development is not commensurate with the urgent need to catch up. 2. PVD coating the basic concepts and characteristics PVD is the English "Physical Vapor Deposition" abbreviation, meaning the physical vapor deposition. We are now generally the vacuum evaporation, sputtering coating, ion plating, and so are called physical vapor deposition. The more mature PVD methods are mainly multi-arc plating and magnetron sputtering in two ways. Multi-arc plating equipment, simple structure, easy to operate. Its ion evaporation source can work by the power supply of the welding machine, and the process of arc starting is similar to that of welding. Specifically, the arc discharge needle contacts and disconnects briefly at a certain process pressure to make the gas discharge . As the cause of multi-arc plating is mainly by means of continuous movement of the arc spot on the surface of the evaporation source to continuously form the molten pool, the metal evaporated, the deposition on the substrate to get the film layer, compared with the magnetron sputtering Not only has high target utilization rate, more metal ionization rate is high, the film and the substrate between the strong binding advantages. In addition, the multi-arc plating coating color is more stable, especially in the TiN coating, each batch are easy to get the same stable golden yellow, so that the magnetron sputtering method catch up. The disadvantage of multi-arc plating is that, when the coating thickness is 0.3μm, the deposition rate is close to the reflectivity, and the film formation becomes very difficult under the condition of low temperature coating with traditional DC power supply. Furthermore, the film surface begins to become hazy. Multi-arc plating Another shortcoming is that, because the metal is evaporated after melting, so the deposition of large particles, low density, wear resistance than the magnetron sputtering film forming poor. It can be seen that multi-arc coating and magnetron sputtering coating have their advantages and disadvantages, in order to give full play to their respective advantages and complement each other, the multi-arc technology and magnetic control technology into one coating machine came into being . In the process of multi-arc plating primer, and then use magnetron sputtering thickening coating, and finally the use of multi-arc plating to achieve the final stability of the surface coating color of the new method. In the late eighties, the emergence of the hot cathode electron gun evaporation ion plating, hot cathode arc
magnetron plasma coating machine, the application is very good, so TiN coated tool quickly universal application. The hot-cathode electron gun evaporates the ion plating, the copper crucible is used to heat and melt the plated metal material, and the tantalum filament is used for heating and degassing the work piece, and the ionization rate is enhanced by the electron gun, not only the TiN coating with thickness of 3-5μm can be obtained, Force, wear resistance are good performance, even with the grinding method is difficult to remove. But these devices are only suitable for TiN coating, or pure metal film. For the multi-layer coating or composite coating, the powerless, difficult to adapt to high-hardness materials, high-speed cutting and mold application diversity requirements. 3. Modern coating equipment (uniform heating technology, temperature measurement technology, unbalanced magnetron sputtering technology, auxiliary anode technology, intermediate frequency power supply, pulse technology) Modern coating equipment mainly by the vacuum chamber, vacuum access part, vacuum measurement part, Power supply part, process gas input system, mechanical transmission part, heating and temperature measurement parts, ion evaporation or sputtering source, water cooling system and other components. 3.1 vacuum chamber coating equipment mainly continuous coating production line and single room coating machine in two forms, due to the mold coating on the heating and mechanical transmission part of a higher demand, and mold shape, size vary widely, continuous coating production line Usually difficult to meet the requirements, to be used single-chamber coating machine. 3.2 Vacuum acquisition part In vacuum technology, the vacuum part is an important part. Due to the high adhesion requirements of the mold coating, the background vacuum before the coating process is better than 6mPa, and the vacuum degree can reach 0.06mPa or more after the coating process is finished. Therefore, a reasonable choice of vacuum access equipment is realized. Vacuum is critical. For now, no pump has been working from atmospheric pressure has been close to ultra-high vacuum. Therefore, the vacuum is not a vacuum equipment and methods can be achieved, we must combine the use of several pumps, such as mechanical pumps, molecular pump systems. 3.3 vacuum measurement part of the vacuum system vacuum measurement part of the vacuum chamber is to measure the pressure. Like a vacuum pump, there is no vacuum gauge to measure the entire vacuum range, so people according to different principles and requirements made of many types of vacuum gauge. 3.4 power supply part of the target power supply are DC power supply (such as MDX), IF power (such as the United States AE company PE, PEII, PINACAL); workpiece itself usually need to add DC power (such as MDX), pulse power Production PINACAL +), or RF power supply (RF). 3.5 Process gas input system Process gas, such as argon (Ar), krypton (Kr), nitrogen (N2), acetylene (C2H2), methane (CH4), hydrogen (H2), oxygen (O2) Gas supply, the gas pressure relief valve, gas cut-off valve, pipeline, gas flow meter, solenoid valve, piezoelectric valve, and then into the vacuum chamber. The advantage of this gas input system is that the piping is simple, crisp, easy to repair or replace. The coating machine does not affect each other. There are also a number of coating machines share a group of gas cylinders, this situation in some of the larger coating workshop may have the opportunity to see. Its advantage is to reduce the amount of cylinder occupancy, unified planning, unified layout. The disadvantage is that, due to the increase in joints, so that the opportunity to increase leakage. Moreover, the coating machine will interfere with each other, a coating machine pipe leak, there may affect the quality of other coating machine. In addition, the replacement of gas cylinders, you must ensure that all the host in a non-gas state. 3.6 mechanical transmission part of the tool coating thickness must be uniform around the same, therefore, in the coating process must have three rotation to meet the requirements. (I), the small work-piece table also rotates (II) and the workpiece itself can rotate at the same time (III) at the same time as the large workpiece table is rotated (I). In the mechanical design, generally in the center of the large workpiece turntable for a large driving gear, surrounded by a number of small Xingxing wheel meshing with the fork and then dial the workpiece rotation. Of course, in the mold coating, there are generally two rotation is sufficient, but the gear can be carried capacity must be greatly enhanced. 3.7 heating and temperature part of the work die coating, how to ensure uniform coating workpiece heating than decorative coating heating is much more important. Mold coating equipment generally have two before and after the heater, with thermocouple temperature measurement and control. However, since the thermocouple clamps
are set differently, the temperature reading can not be the true temperature of the workpiece. To measure the true temperature of the workpiece, there are many ways, here describes a simple surface thermometer method (Surface Thermomeer). The working principle of the thermometer is that when the thermometer is heated, the bottom of the spring will be thermal expansion, so that the pointer to promote the positioning of the pointer rotation until the maximum temperature. When cooling, the spring contraction, the pointer reverse rotation, but the positioning pointer is maintained at the highest temperature position does not move, open the door, read the temperature indicated by the positioning indicator, which is the vacuum chamber heating, the surface thermometer placement has reached the highest Temperature value. 3.8 ion evaporation and sputtering source The multi-arc plating evaporation source is generally round cake shape, commonly known as round cake target, in recent years also appeared in a rectangular multi-arc target, but no significant effect. Round cake target mounted on the copper target (cathode seat) above, both for the rib connection. The target is equipped with magnets, by moving the magnet back and forth to change the magnetic field strength, adjustable arc movement speed and trajectory. In order to reduce the temperature of the target and the target, the target to continue to pass into the cooling water. In order to ensure high thermal conductivity and thermal conductivity between the target and the target, a tin (Sn) gasket may be applied between the target and the target. Magnetron sputtering coating is generally rectangular or cylindrical target, 3.9 water-cooled system because the mold coating, in order to improve the rate of metal ionization, the cathode target are as much as possible to use a large power output, the need for adequate cooling , And many of the coating in the mold coating, heating temperature 400 ~ 500 º C, the vacuum chamber wall, the cooling of the sealing surface is also important, so the best cooling water is about 18 ~ 20 º C cold water Machine water supply. The water cooling system should be able to switch to the hot water state about 10 minutes before the door is opened. The hot water temperature is about 40-45 ºC, in order to prevent the contact between the vacuum chamber wall and the cathode target and the hot air. 4. Tooling PVD PVD process steps can be briefly described as: IQC → pre-processing → PVD → FQC, were introduced as follows. 4.1 IQC IQC (In Quality Control) The main work In addition to the number of regular inventory, check whether the drawings and the physical match, you must carefully examine the workpiece surface, especially the edge of the cracks and other defects in the site. Sometimes for some knives, knife blade edge, in the body microscope observation, more convenient to find the problem; In addition, IQC staff also pay attention to check whether the plastic parts to be coated, low melting point solder, etc., these things if missed And mixed with the coating process, will be a serious deflation in the vacuum chamber, the light caused by the whole batch of products from the coating, the weight of the original OK product scrapped, the consequences could be disastrous. 4.2 pre-treatment process (steam gun, sandblasting, polishing, cleaning) The purpose of pre-treatment is to purify or rough surface. Purification is to remove all kinds of surface contamination, the preparation of clean surface. Usually, various cleaning agents are used to perform the purification by mechanical, physical or chemical means. Coarsening, in contrast to photoresist, is intended to produce a rough surface to enhance the structural strength of the spray coat or paint finish. We now have the main pre-treatment methods: high temperature steam cleaning, cleaning, sandblasting, grinding, polishing and other methods. 4.2.1 High temperature steam cleaning At present, PVD workshop commonly used high-temperature steam cleaning equipment is steam gun. Its maximum operating temperature of up to 145? C, air pressure in the 3 to 5 bar or so. As the mold often with a number of small holes, threaded holes, holes are often oil, residual coolant and other impurities, with conventional cleaning method is difficult to remove. At this point, high-temperature steam cleaning equipment can maximize its superiority.
4.2.2 cleaning the mold cleaning process before the factory as follows: 1. Ultrasonic dewaxing → 2. Over water → 3. Ultrasonic degreasing → 4. Over water → 5. Ultrasonic from the change → 6. Water → 7 . → 8. Dry air drying the specific implementation, and we are familiar with the decorative coating before cleaning there are many different. This is because the decorative coating of the substrate are mostly stainless steel or titanium alloy, not easy to rust. In addition, the decorative coating on the watermark, mole and other defects is absolutely not allowed. Therefore, the decorative coating on the water quality is very high, even to 15MΩ or more. To ensure high-quality cleaning, can be repeated cleaning, and high-quality pure water plus ultrasonic soak for a long time to get. However, the mold cleaning is different, especially some hot die steel, if the decorative coating as to clean, it will rust a mess. Since the original surface condition of the mold coat is generally rough compared to the decorative coating except for some high standard mirror molds, the surface condition after coating is not as high as that of the decorative coating, We take a quick over-water, dry with oil-free compressed air drying, and then the mold strong wind drying method to deal with. And those high standard mirror mold, generally are 136 and other stainless steel, you can use decorative coating cleaning method. All in all, the mold before the coating method for cleaning the mold used by the different materials vary, due to the mold surface coating before the state varies, and can not be stereotyped. The following is a few kinds of rust from easy to difficult to sort, for reference:
Stainless steel, carbide, cermet alloy, DC53, high speed steel, 8407 There is an automatic washing machine model CR288, produced in Germany. The machine a maximum cleaning capacity of 80KG, mainly for cleaning tools, small parts, or small size of the mold. It has a total of three cleaning tank, the solution inside were tap water + cleaning agents, tap water, deionized water. In addition to the common ultrasonic, flood flushing, spray, swing, hot air drying and other functions, the machine has the advantage of the last with a vacuum step, you can make the water evaporated as soon as possible. Automatic cleaning machine memory of ten kinds of technology, by the supply side pre-set. One to nine can be used for different types of products, different surface state of the purification process. Tenth for the filling cleaning agent. 4.2.3 sandblasting sandblasting method is the use of compressed air abrasive strong scouring the surface of the workpiece, thereby removing rust, carbon deposition, welding slag, oxide, residual salt, the old paint and other surface defects. By abrasive use conditions, sandblasting is divided into dry sandblasting and wet sandblasting two categories. Sandblasting of the main parameters of the gun from the angle, the rotation speed of the clamping table, moving speed, travel, round-trip times, sandblasting time, sandblasting pressure. We have used the parameters of a gun from: 30 ~ 70mm; Inclination 30 ~ 70? C; Clamping table rotation speed of 10 to 30; from 3 to 9 times the number of sandblasting pressure: 1.8 to 3.5 bar and so on. Specific operation, according to the degree of surface dirt, workpiece hardness, workpiece surface geometry and other factors, select the upper and lower limits. We used in the dry sandblasting machine for the abrasive glass beads, suitable for spraying some of the hardness of the material, such as oil, mold, etc .; in the liquid abrasive sanding machine used in the abrasive for the alumina, high hardness, suitable Spray some high hardness materials, such as cemented carbide materials. The abrasive grain size used for sand blasting is also important for tooling coatings. If the abrasive particle size is too large, the workpiece surface is too rough; if the abrasive particle size is too small, will reduce the impact force, and even embedded in the workpiece surface, cleaning difficult to remove, so that the workpiece coating adhesion decreased. To this end, some countries in Europe, the mold before the sandblast abrasive abrasive particle size used to do a careful study to be strict to ensure that more than 85% of the grain size in the A, B two-point range can be used. In contrast, China's abrasive suppliers also lack the consensus in this regard, we rarely do this test. 4.3 PVD
coating process (heating, ion cleaning, coating, cooling, process gas, barometric pressure, temperature, sputtering power) 4.4 FQC FQC English spelling is: "Function Quality Control", which means functional quality control Not with the general sense of the OQC (Out Quality Control). FQC content includes visual inspection, layer depth inspection, adhesion inspection, wear resistance inspection, corrosion resistance inspection, simulation test and other methods. I plant the current application of the main visual inspection, layer depth inspection and adhesion checks. Since most of the products we are exposed to are not allowed to do destructive inspection, so we in the coating, each
batch will be placed into the batch with the sample. When doing a layer depth check and an adhesion check, in most cases, the following sample is actually inspected. Because the sample and the product in the raw materials, heat treatment status, clamping position, etc. are difficult to agree, so the detection of the results, and the actual value of the product will have some errors. Sometimes there may be considerable error, can only do reference to use. Of course, if necessary, we can also produce analog parts to achieve the purpose of accurate measurement.
4.4.1 Appearance inspection
After picking the door for the product, should carefully check the surface without cracks, off the coating, loose and other defects. For the tool, knife particles, need to
carefully check their microscope under the edge of the state. 4.4.2 Layer depth inspection layer depth examination with slices metallographic observation, X-ray inspection method, using monochromatic light as light source optical test method, ball mill test method and other methods. The depth of the mold coating is measured on a ball mill. Method is to use a diameter of 10mm ball with the test surface of the roller, and then under the microscope to measure the wear marks of the relevant data into the formula, you can easily calculate the layer depth. The depth of this method is characterized by: easy to apply, the error is slightly larger. But the error applied to the above model will not be too much impact. Interested colleagues can also refer to the relevant instructions. Adhesion inspection methods are many, each factory according to the characteristics of their products, have developed a corresponding detection method. Among them, there are two more authoritative methods, one is in the Rockwell hardness, the cone-type indenter indentation indentation test done under the microscope to observe the number of cracks around the indentation to determine the coating adhesion High and low. The method requires a very high shape of the diamond indenter, not only the center of the circle in the center, but also the circularity of the diamond cone must be very regular. Unfortunately, at present, China does not yet have its national or industry standards; another method is the scratch method, some of our earlier research department launched the coating is also used in the method, there are special national industry standards available Inquire. 5. Coating process (sandblasting, grease coating technology, polishing treatment) 7. Detection technology (detection of adhesion, depth of detection, acid etching) 8. Coating stripping technology (TiN / TiAlN stripping technology, CrN / DLC / CrAlTiN stripping technology, carbide surface coating stripping technology) 9. Coating tool application technology (the correct choice of coating, coating the correct use of the tool coating on the tool Highly optimized, high-speed machining can result in higher temperatures, resistance to oxidation and hardening due to the higher temperatures generated by conventional cutting processes. For example, chromium nitride (CrN) Friction coefficient, improve the smoothness and chip removal situation.
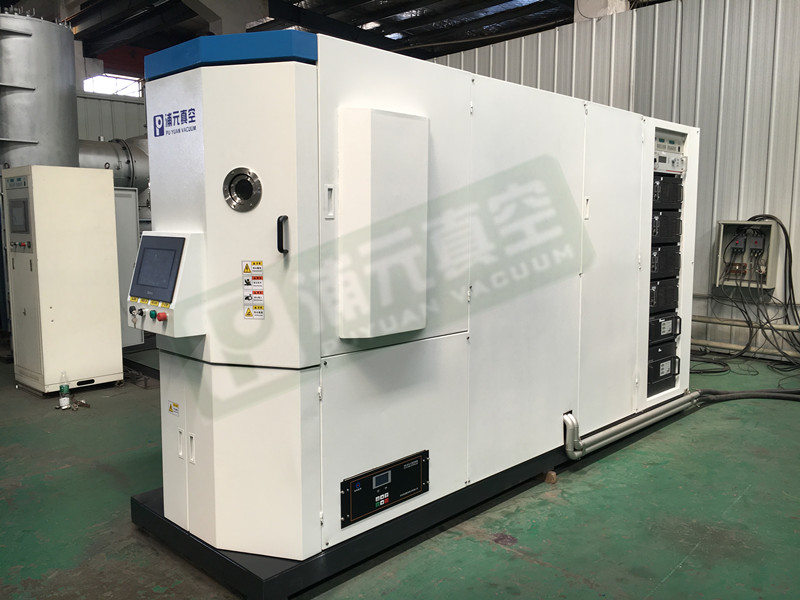